Field-tested solutions
with proven results
Discover a variety of solutions for energy, process, and production optimization, created in collaboration with our leading industry partners.
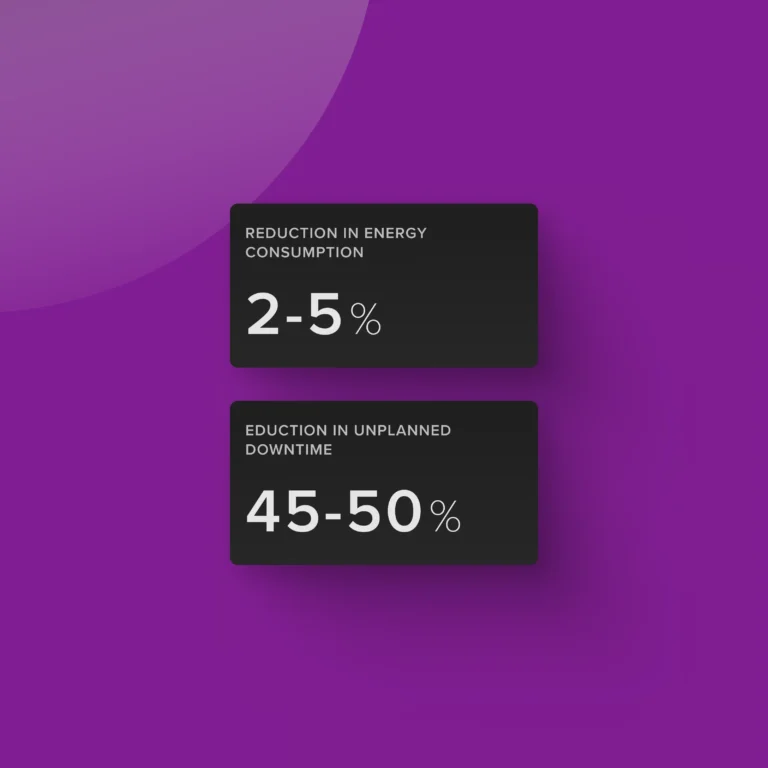
Performance Optimization in Process Compressors
Edit Content
Performance Optimization in Process Compressors
Challenge
- Unplanned downtimes lead to reactive and time-based maintenance which can be costly and inefficient
- Difficult to quantify metrics that correlate to valve health
Solution
- Use first principles to predict the efficiency and power in real-time
- Develop ML model to predict the anomalies in real-time leading to sub-optimal operations
- Email notifications for real-time deviations
- Recommendations to close the loop for optimal operations
Result
- 2-5% reduction in energy consumption
- 45-50% Reduction in unplanned downtimes
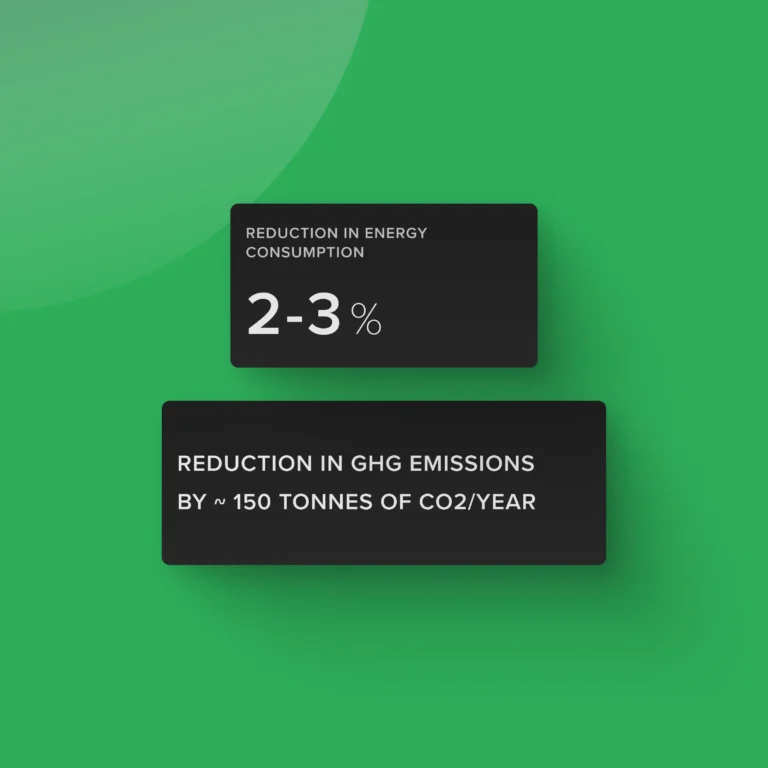
Performance Optimization in Air Compressors
Edit Content
Performance Optimization in Air Compressors
Challenge
- More than required energy consumption due to sub-optimal operations
- Unnoticed deviations and losses in the compressed air network leading to excessive energy consumption
Solution
- Predicting the Performance and Health score of the compressors with early warnings
- Using process and mechanical parameters to predict the Ideal energy consumption against the actual consumption
- Email notifications for real-time deviations
- Recommendations to close the loop for optimal operations
Result
- 2-3 % reduction in energy consumption
- Reduction in GHG emissions by ~ 150 Tonnes of CO2/year
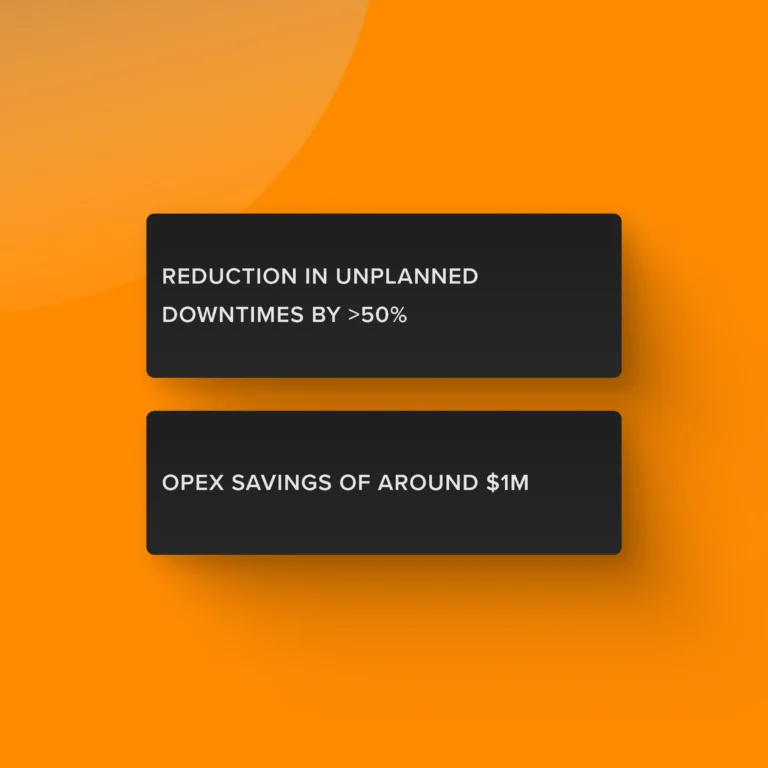
Performance Optimization for Heat Exchanges
Edit Content
Performance Optimization for Heat Exchanges
Challenge
- Fluid with dissolved impurities upon reaching saturation deposit on the inner tubes causing scaling
- Scaling was leading to corrosion and improper heat transfer
Solution
- Using ML to create a PdM model to allow personnel to take necessary action before reaching impurities saturation
- Parameter creation of Overall Heat transfer Coefficient(U) that varies with time
- Employing physics-based features to predict fouling
Result
- Reduction in unplanned downtimes by >50%
- Savings of around $1M
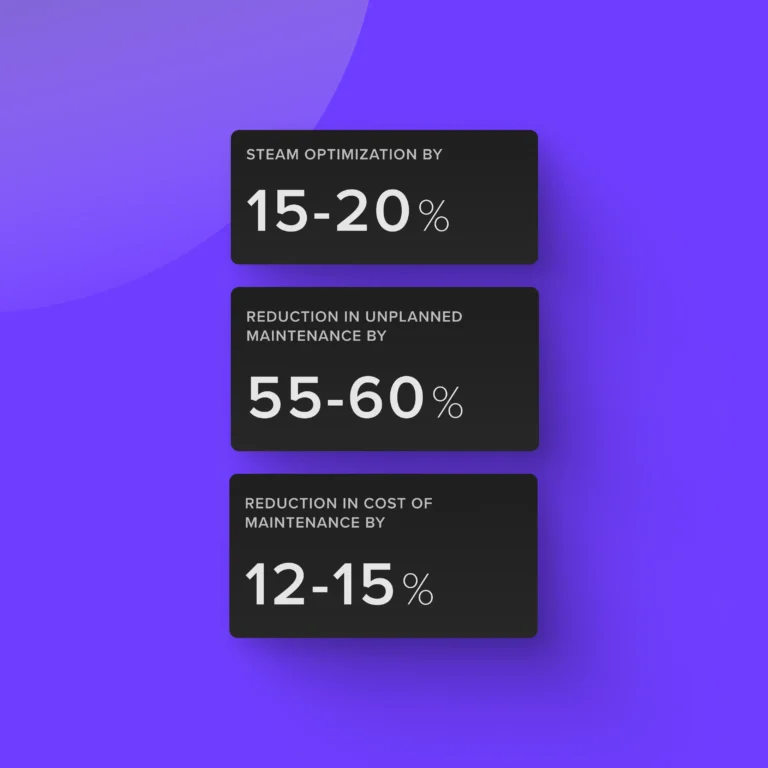
Multi-effective Evaporator – Steam Optimization
Edit Content
Multi-effective Evaporator – Steam Optimization
Challenge
- Includes frequent thermal breakdowns due to fouling
- More than required steam consumption leading to sub-optimal operations
Solution
- Create a soft sensor for overall heat transfer coefficient and set alarm limits
- Benchmark and compare the real-time steam consumption with respect to the ideal consumption
Result
- Steam optimization by ~ 15-20%
- Reduction in unplanned maintenance by 55-60%
- Reduction in cost of maintenance by 12-15%
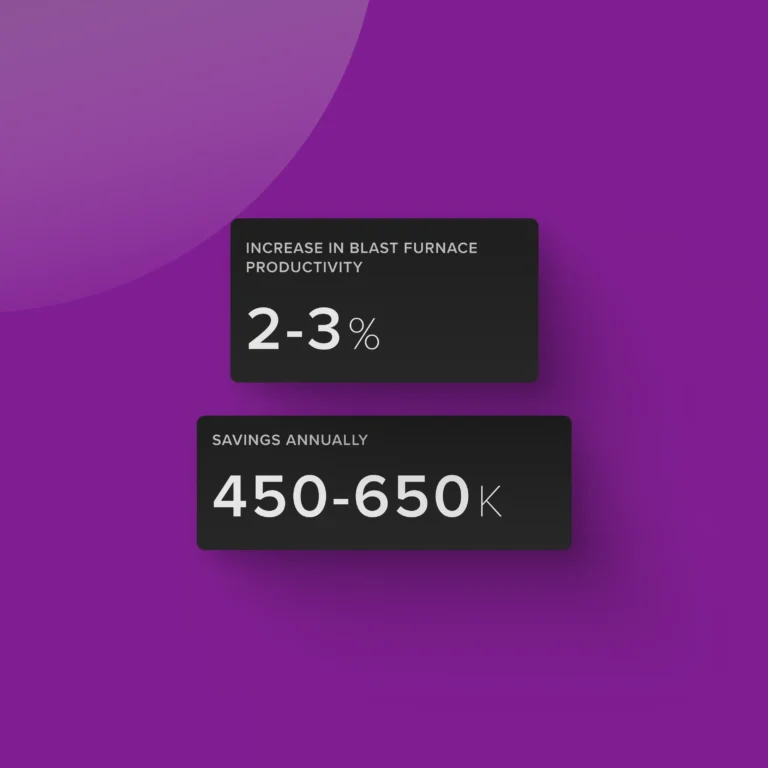
Productivity Improvement Blast Furnace Operations
Edit Content
Productivity Improvement Blast Furnace Operations
Challenge
- Complex and dynamic conditions with various parameters makes it difficult to detect hanging incidents in real-time
- Difficult to monitor Silicon content of the molten iron which is an important indicator of the furnace temperature variations
Solution
- ML based models to predict the deviations in the furnace operations – correlated with hanging
- Predict silicon content in real time using the historical data
Result
- 2-3% Increase in blast furnace productivity
- ~ 450-600k Savings annually
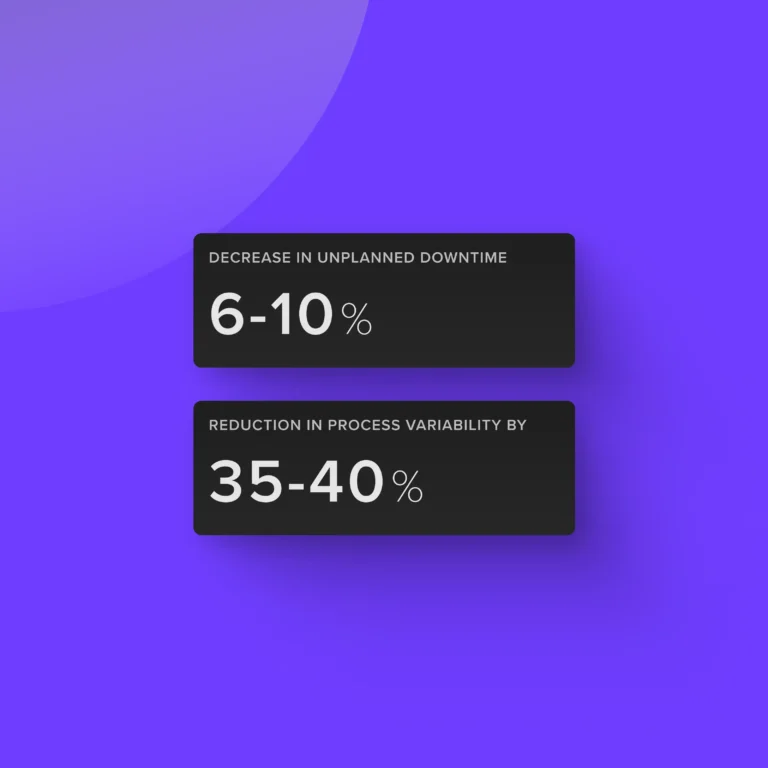
Feed Strategy Optimization in Aluminum Smelters
Edit Content
Feed Strategy Optimization in Aluminum Smelters
Challenge
- Difficult to maintain the bath temperature and excess ALF3 in the specified range
- Shift engineer experience driving ALF3 addition directly impact the performance of the smelters productivity
Solution
- Advanced Conditioning for identifying the deviations in the bath temperature and excess ALF3
- Used historical data to model the required ALF3 feed to be added for optimal operations
Result
- 6-10% decrease in unplanned downtime
- Reduction in process variability by 35-40%
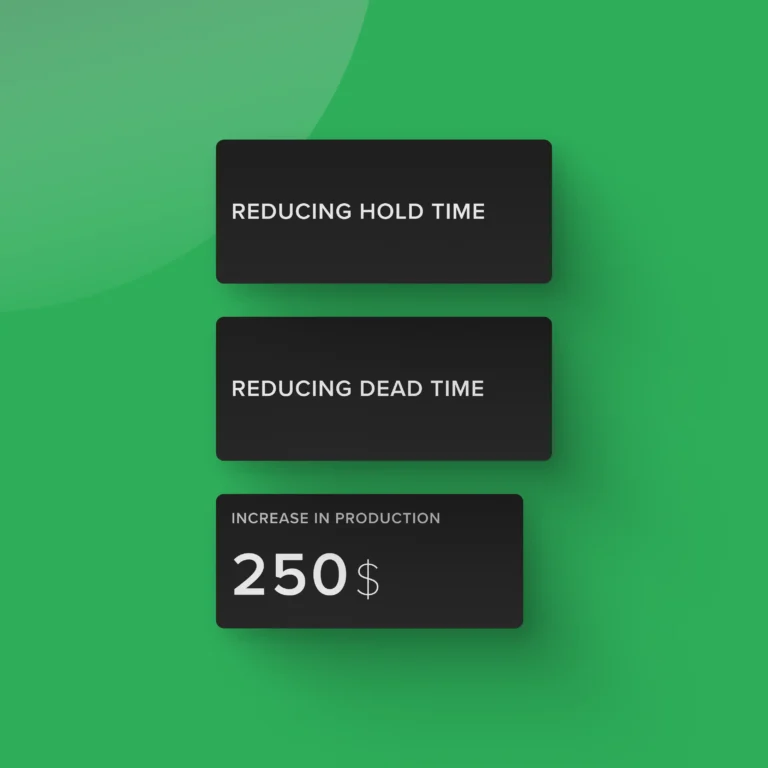
Furnace Efficiency Prediction
Edit Content
Furnace Efficiency Prediction
Challenge
- Ethylene furnaces coke (foul) during cracking operations resulting in a loss of efficiency
- Improper decoking resulting in equipment damage and lost production time
Solution
- Identify different phases of decoke operation and excessive hold times
- Predict decoke effectiveness with KPIs like temperature recovery and run time between decokes
Result
- Tracking decoke effectiveness metrics identified procedural inefficiencies and inconsistency in execution
- Optimization of decoke procedures reducing hold time and dead time has resulted in an additional $250k/y in production.
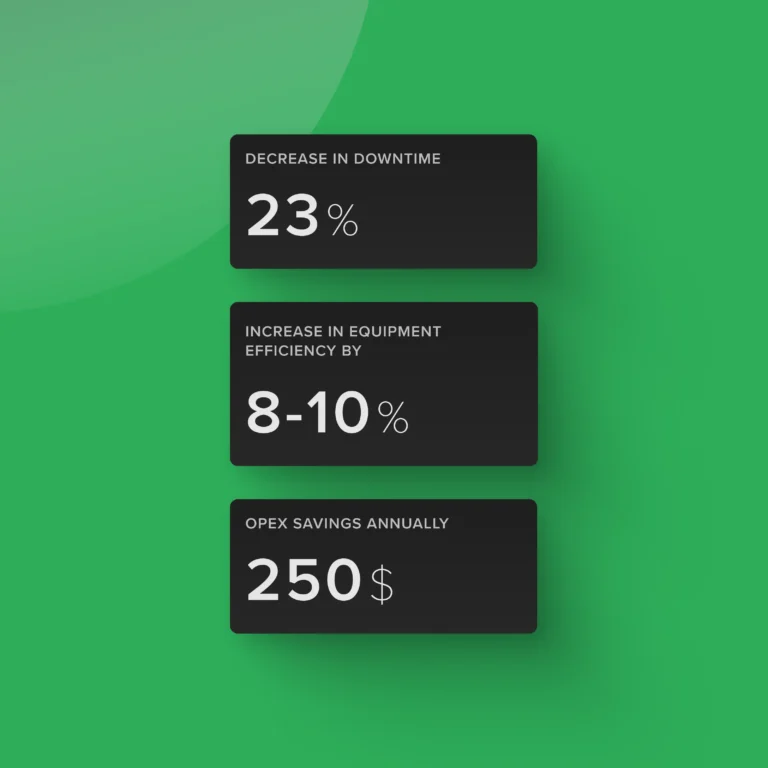
Distillation Column Efficiency
Edit Content
Distillation Column Efficiency
Challenge
- Changes in feed quality impact the efficiency of columns
- Frequent vacuum pumps/ reboilers and condenser failure causes operational upsets
Solution
- ML-algorithm based PdM model for vacuum pump and reboiler
- Employing Data Analysis to understand trends and create indicators to drive predictions
- Employing first-principle based equations to understand status of machine
Result
- 23% decrease in downtime
- Increase in efficiency by 8-10%
- ~ 250k Savings annually
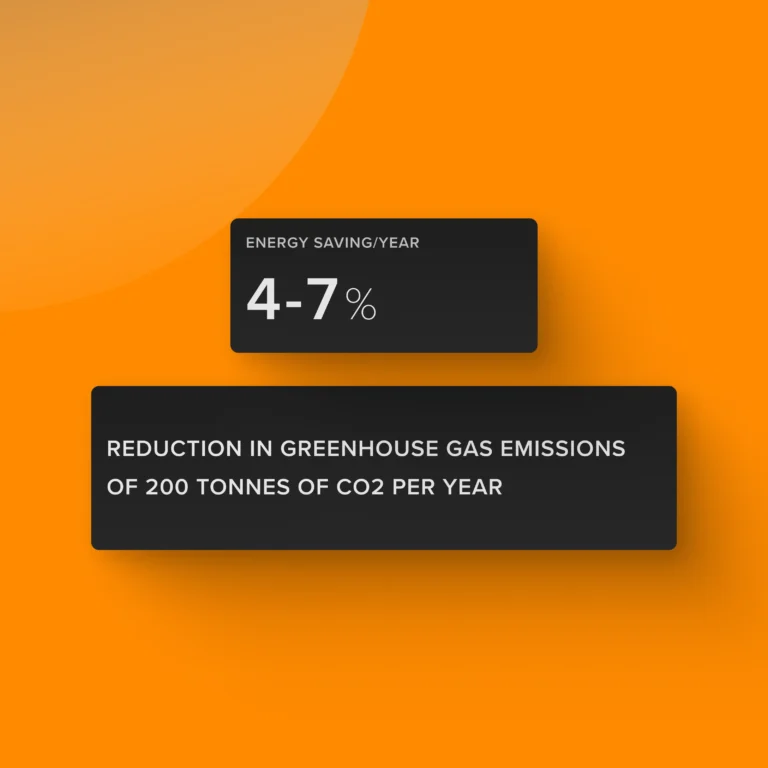
Boiler Efficiency Prediction
Edit Content
Boiler Efficiency Prediction
Challenge
- High variations in fuel quality and feed leads to operational challenges in maximizing the steam generation
- Degradation of boiler efficiency leading to suboptimal combustion strategies
Solution
- Maintaining enthalpy balance in boilers for incoming streams and generated steam to track the efficiency in real-time
- Predicting the efficiency degradation and recommending the corrections to counter impact the fuel quality variations
Result
- Optimal Steam to fuel ratio
- 4-7 % energy savings/ year
- Reduction in greenhouse gas emissions of 200 tonnes of CO2 per year
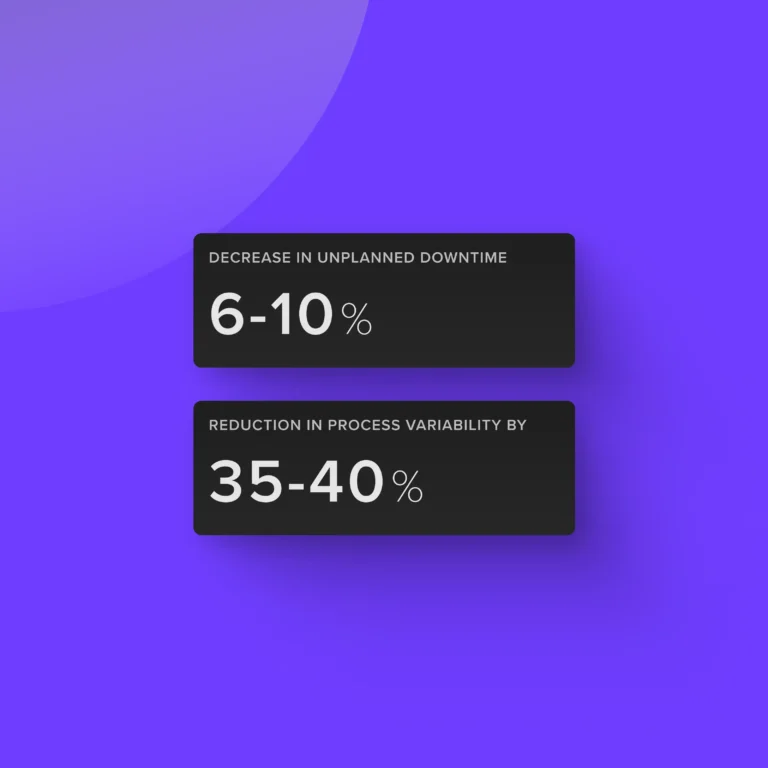
Cooling Tower Health Monitoring
Edit Content
Cooling Tower Health Monitoring
Challenge
- Impact of seasonality and load requirements are unknown
- More than required energy consumption in fan, water losses
Solution
- Predict the energy requirements using advanced modeling to regulate the fan RPM
- Monitor and track the losses – evaporative, drift and blowdown of the water stream
Result
- Timely and effective maintenance for cooling towers
- Increased efficiency by 12-16%
Need a custom solution?
Please reach out if you need more details on a custom solution tailored to your specific needs. We collaborate with leading industry partners who have extensive experience developing with Kelvin for real-world applications.